
Optimize Logistics with AGV Solutions
Leverage Automated Guided Vehicles (AGVs) to streamline warehouse workflows, reducing error rates by 25% and boosting throughput by up to 30%, enabling seamless integration with existing systems.
Precision and Efficiency with AGV Technology
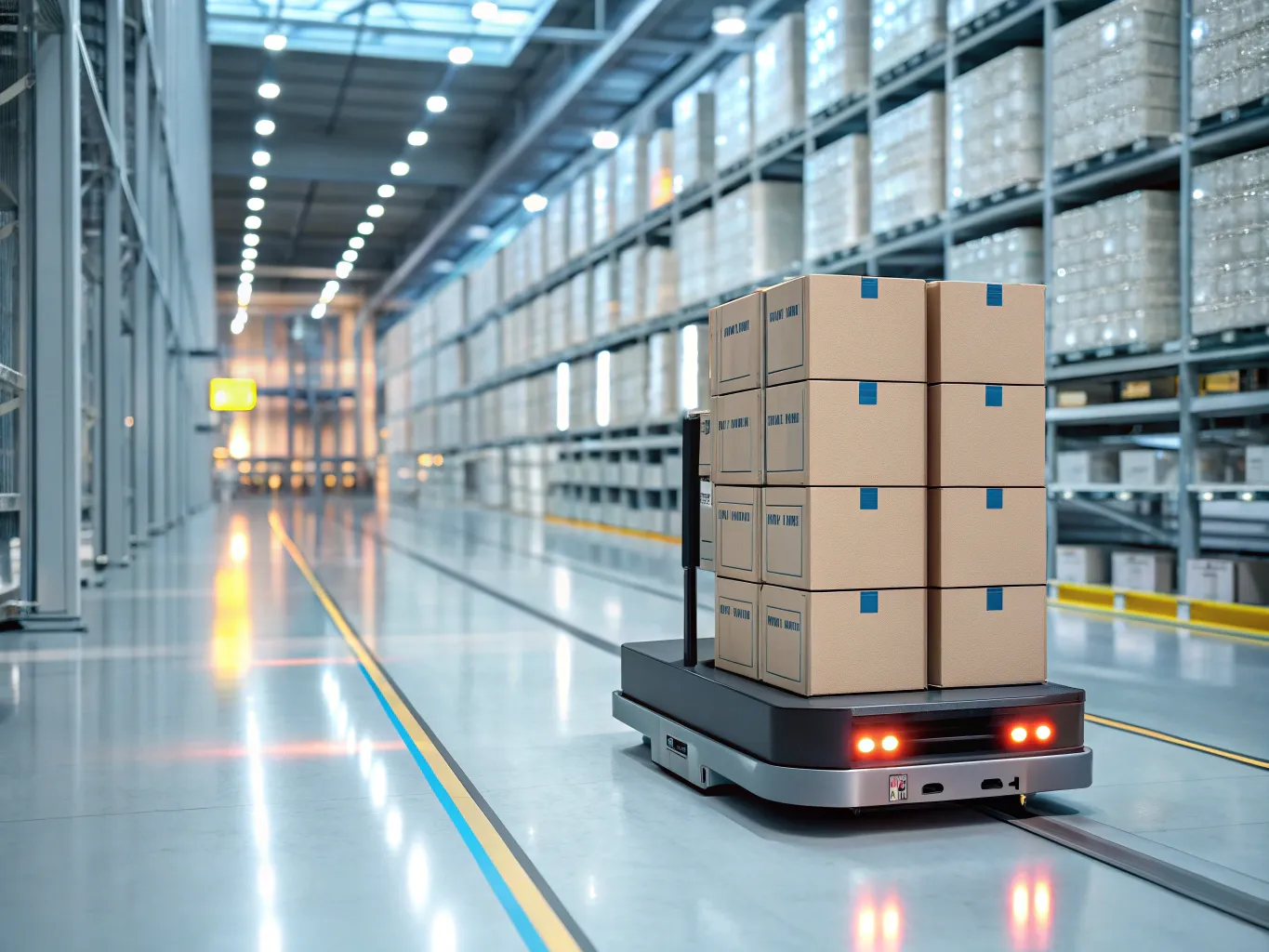
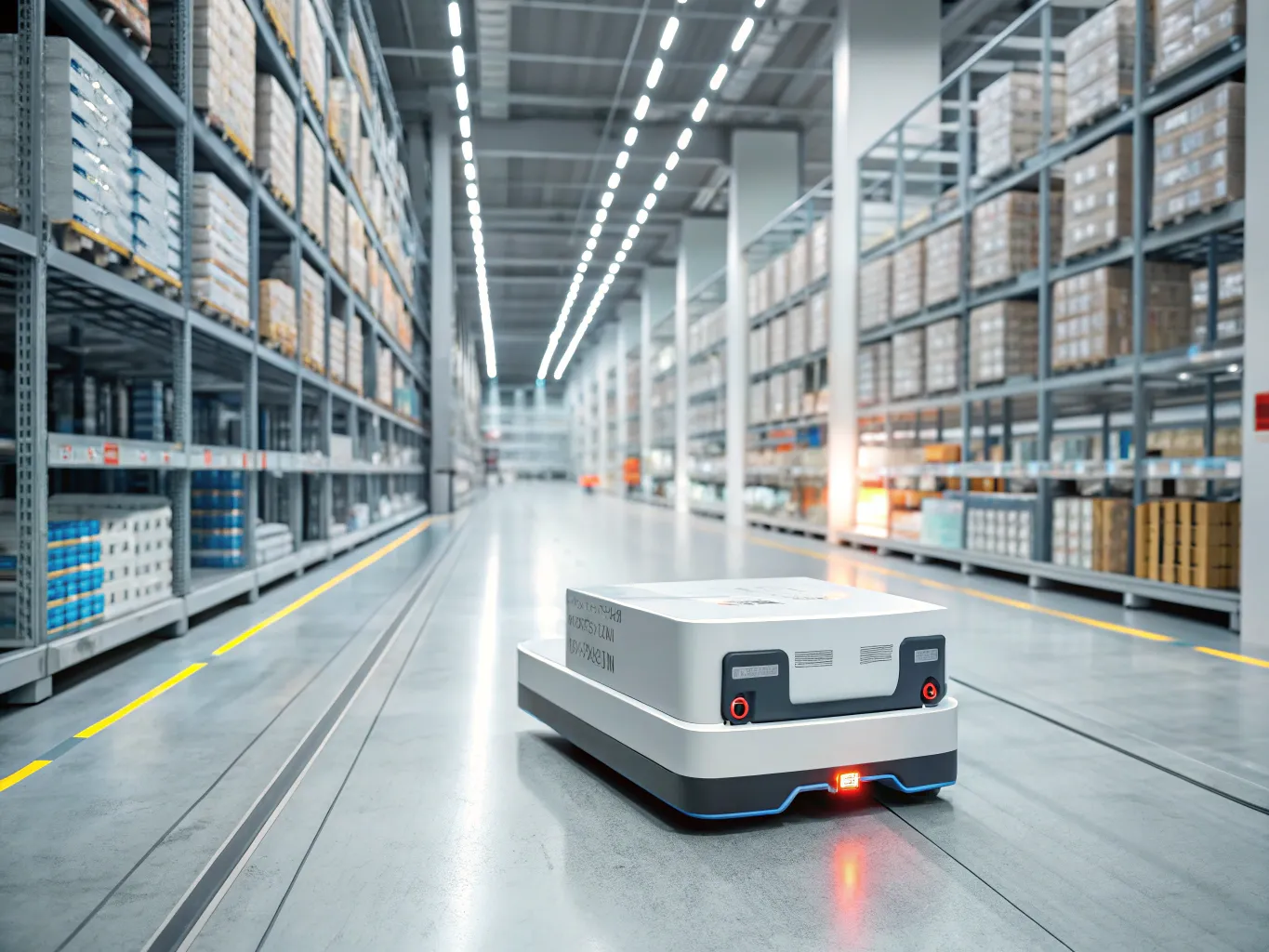
Maximize Facility Efficiency
Diverse Applications of AGV Technology
- Manufacturing: AGVs facilitate just-in-time delivery of components, reducing production downtime by up to 30%. They seamlessly integrate with robotic arms on assembly lines, enhancing precision and maintaining consistent production flow.
- Warehousing: AGVs autonomously manage inventory transport, from storage to shipping, decreasing manual handling needs. This results in a 25% increase in order accuracy and allows for efficient use of vertical storage space.
- Distribution: In distribution centers, AGVs streamline cross-docking processes by rapidly transferring goods between vehicles, cutting turnaround time by over 40% and enhancing supply chain throughput.
- E-commerce: AGVs enhance the speed and accuracy of order fulfillment. By handling repetitive tasks like picking and packing, they boost efficiency by up to 50%, meeting rapid delivery demands of online retail.
- Retail: In retail environments, AGVs manage in-store logistics, such as shelf restocking and backroom inventory movement, ensuring timely replenishment and improving stock visibility by 35%, enhancing customer satisfaction.
Advanced Features of AGV Technologies
- Laser Navigation: Utilizes highly precise laser scanners to determine exact positioning within 0.5 centimeters, ensuring seamless navigation in complex warehouse environments, reducing route errors by up to 30%.
- Line Following: Employs sensors to detect and follow predefined paths marked on facility floors, offering a cost-effective solution for facilities with repetitive movement patterns, enhancing delivery cycle consistency by 20%.
- Obstacle Detection: Equipped with real-time sensors to identify and respond to dynamic obstacles, reducing collision risks by over 40% and ensuring uninterrupted operations in bustling logistics hubs.
- RFID Tracking: Integrates RFID technology to track inventory and manage asset locations with pinpoint accuracy, improving inventory management efficiency by 25%, and minimizing lost or misplaced goods.
- Vision Systems: Leverages high-resolution cameras and advanced algorithms to detect environmental changes and adjust routes dynamically, enhancing flexibility and adaptability in rapidly changing environments, boosting route efficiency by 15%.
Key Features of AGVs
Automated Loading
Our AGVs enhance operational efficiency by autonomously loading and unloading pallets, reducing manual labor needs by up to 30%. This automation minimizes human error and increases throughput, allowing facilities to handle an additional 200 pallets per shift.
Intelligent Routing
Utilizing advanced AI algorithms, AGVs dynamically adjust their routing in real-time to minimize congestion and maximize delivery speed. This capability decreases travel time by 20%, ensuring timely deliveries even in high-traffic zones within the facility.
Safety Systems
Equipped with LIDAR-based obstacle detection and emergency stop capabilities, AGVs prevent collisions and enhance workplace safety. These features have reduced incident rates by 40%, fostering a safer environment for both machinery and personnel.
24/7 Operation
Engineered for continuous operation, our AGVs support around-the-clock productivity, crucial for meeting tight production schedules. With a 99% uptime, they ensure minimal disruption, allowing companies to increase their operational output by 15% annually.
Optimizing Fleet Management with AGVs
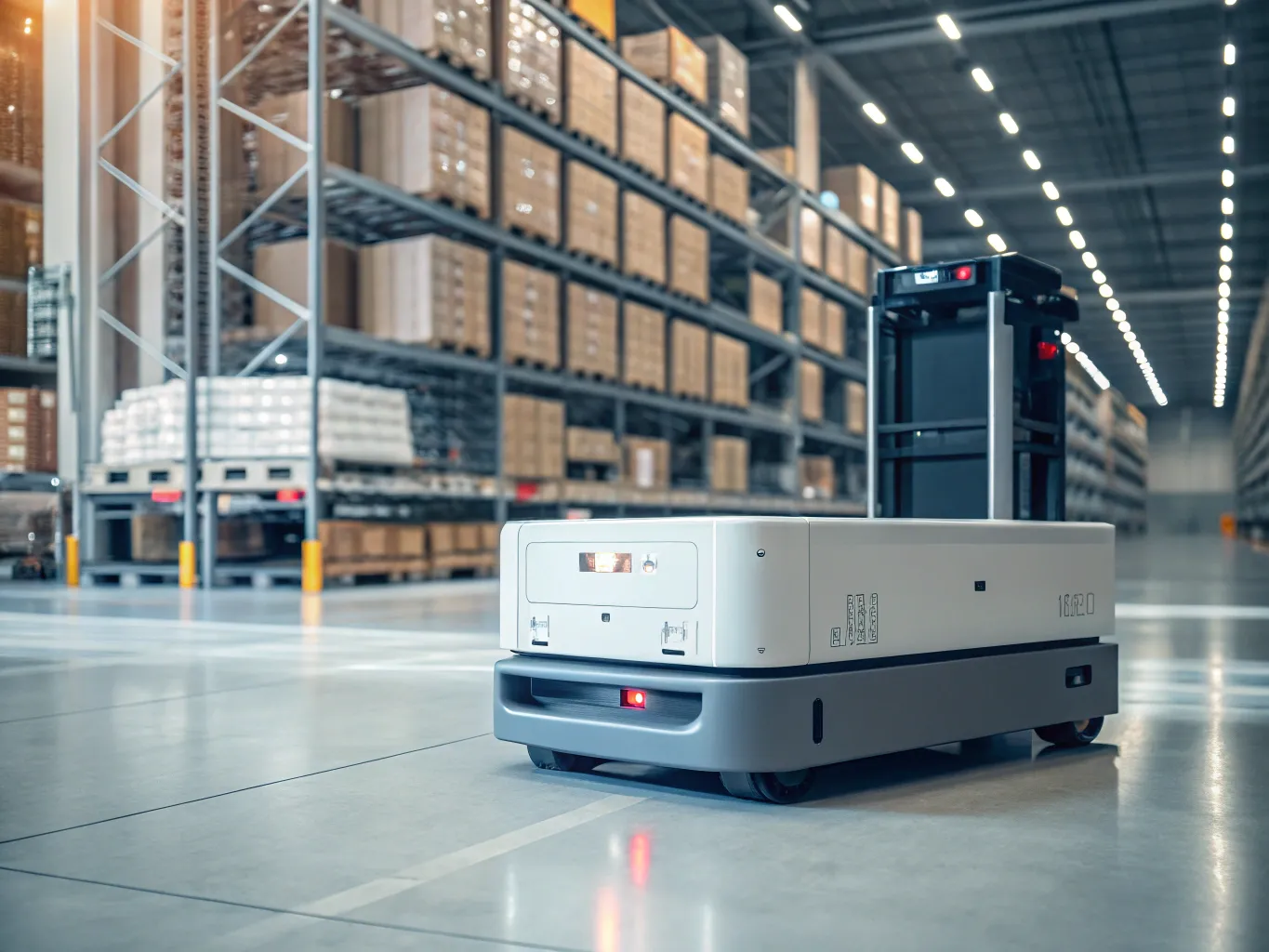
Comprehensive Benefits of AGVs
- Enhanced Productivity: Automated Guided Vehicles (AGVs) increase material handling speeds by up to 30%, enabling faster completion of tasks. For example, in a high-volume distribution center, AGVs ensure continuous operation without breaks, resulting in increased throughput and faster order fulfillment times.
- Reduced Labor Costs: By automating repetitive tasks, AGVs can decrease labor costs by approximately 20%. In a large-scale warehouse, this enables human resources to be redirected towards more strategic roles such as quality assurance and process optimization, contributing to overall business growth.
- Consistency in Quality: AGVs deliver precise and repeatable processes, ensuring consistent quality in material handling. For instance, in pharmaceutical environments, AGVs maintain strict compliance by following exact routes and handling protocols, reducing the risk of contamination and errors.
- Flexible Implementation: AGVs are adaptable to various layouts without requiring major infrastructure changes. A retail company can deploy AGVs across different store formats to handle inventory restocking, allowing for seamless operations during peak seasons or store upgrades.
- Scalable Solutions: As business needs evolve, AGV systems can be easily scaled up by integrating additional units. For example, an e-commerce warehouse can gradually expand its AGV fleet to manage increased demand during holiday seasons, ensuring capacity aligns with sales peaks without disrupting current operations.
Tailored AGV Integration Solutions
Your Path to Automation
You may also be interested in
Maximize your potential with our seamless, end-to-end supply chain solutions.
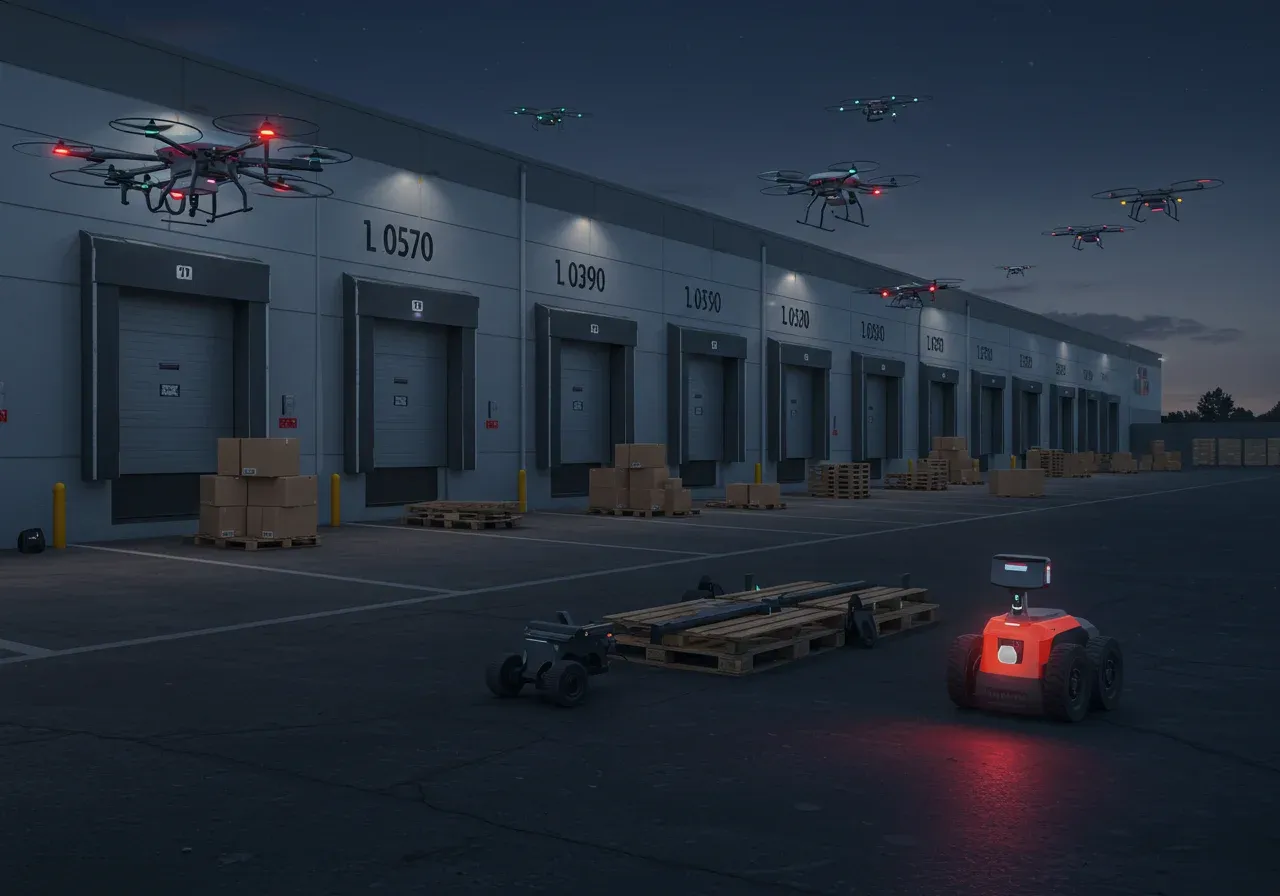
Automation
Leverage state-of-the-art automation to optimize logistics, boosting operational accuracy by up to 30% while minimizing human error. Enhance supply chain agility and cut transit times significantly.
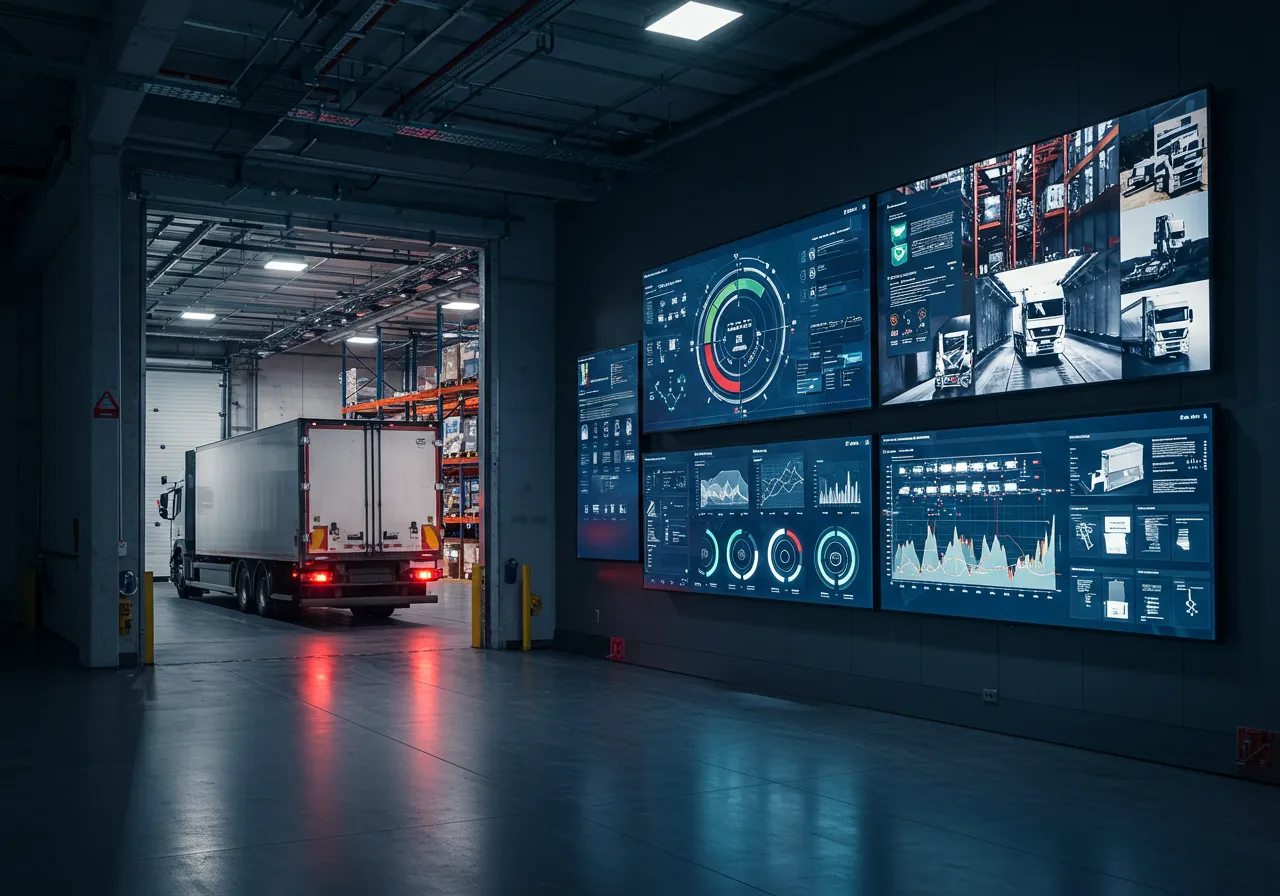
EDI
Enhance accuracy and speed in transactions by integrating EDI, reducing manual errors by up to 90%. Elevate supplier and partner interactions with seamless data exchange, driving efficiency across your logistics network.

Customer Relationship Management (CRM) Integration
Transform your logistics with seamless CRM integration. Improve customer interaction efficiency by 30%, increase order accuracy, and reduce response times, leading to higher customer satisfaction.