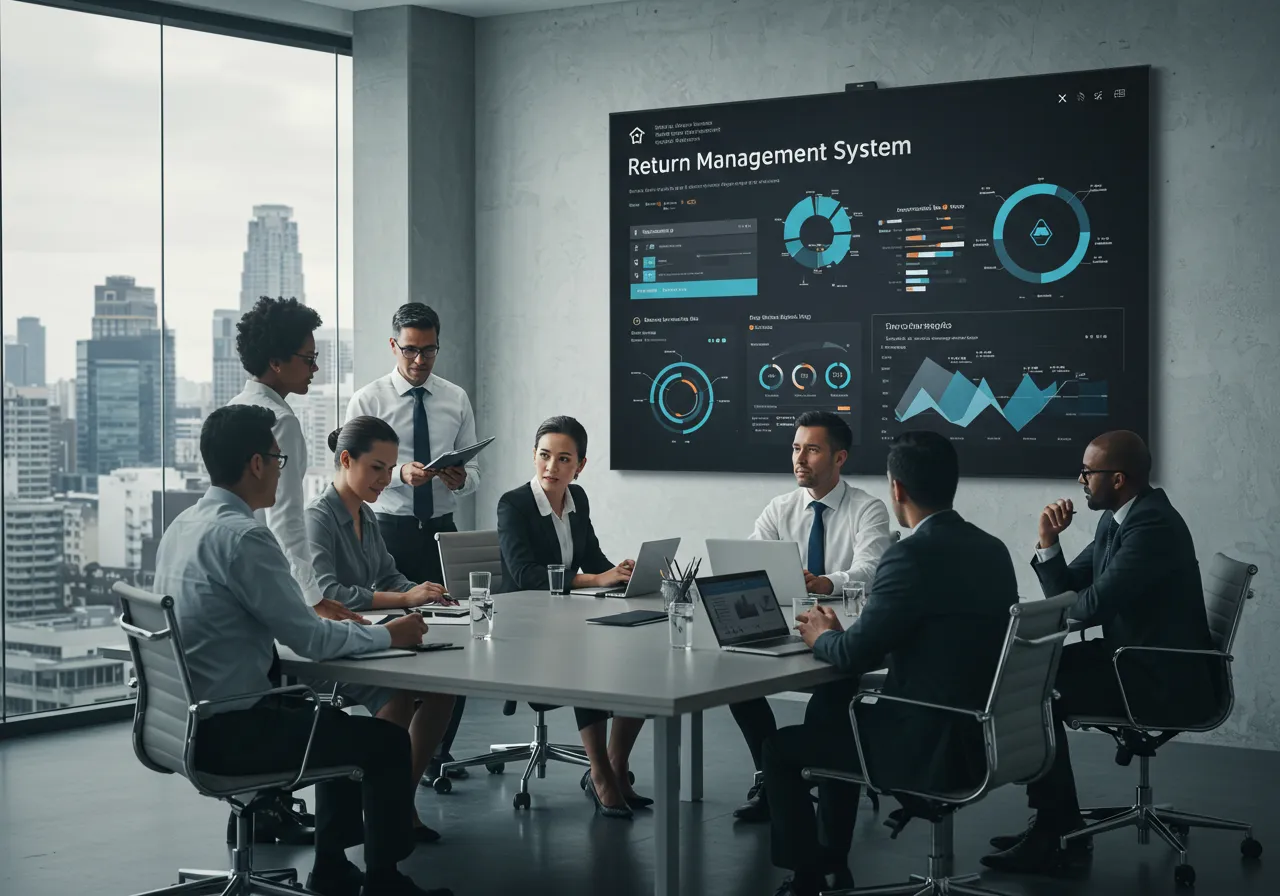
Streamline Returns with RMS Technology
Efficiently manage returns to boost operational efficiency, enhance customer loyalty, and cut processing time by up to 30%. Achieve seamless returns with our sophisticated RMS tools.
Optimizing Returns with AI-Driven RMS
-right-image-1744329644.webp)
-left-image-1744329674.webp)
Automated Return Tracking Solutions
Industries We Serve with Precision Logistics
- Retail: Enhance in-store inventory management by reducing stockouts by up to 35% and improving product availability through seamless restocking processes, ensuring high customer satisfaction and increased sales.
- E-Commerce: Streamline order fulfillment processes with a robust integration of ERP systems, resulting in a 40% reduction in delivery times and a 25% increase in order accuracy, enhancing customer trust and repeat business.
- Manufacturing: Optimize supply chain operations by implementing just-in-time inventory techniques, cutting excess inventory costs by 30% and improving production scheduling for faster turnaround times and higher efficiency.
- Logistics: Provide real-time shipment tracking and data analytics to enhance route optimization, reducing fuel costs by 15% and improving delivery reliability for better customer service and operational savings.
- Warehousing: Implement advanced warehouse management systems (WMS) to increase picking efficiency by 50% and reduce error rates significantly, leading to streamlined operations and improved productivity across the warehouse.
Core RMS Features: Enhancing Reverse Logistics
- Return Tracking: Leverage GPS-enabled tracking systems to monitor returns in real-time, reducing processing time by up to 30% and increasing accountability across your supply chain. This ensures accurate data collection and boosts transparency, which is crucial for industries like electronics where precise tracking is essential.
- Cost Analysis: Utilize advanced financial modeling to evaluate return costs and identify potential savings. Implementing machine learning algorithms can predict cost trends, allowing for a 15% reduction in unnecessary expenses, vital for maintaining competitive pricing in the competitive retail sector.
- Inventory Restock: Use automated systems to promptly update inventory records post-return, minimizing stockouts and overstock scenarios. This feature is crucial for apparel companies, where a rapid restock process can lead to a 25% increase in sales opportunities during high-demand periods.
- Customer Feedback: Integrate AI-driven sentiment analysis to process customer feedback efficiently, helping to improve product quality and customer satisfaction. This feature yields a 10% boost in repeat customer purchases, as seen in the home appliance industry, where customer input directly influences product development.
- Analysis and Reporting: Deploy comprehensive dashboards that offer real-time analytics on return trends, helping businesses make data-driven decisions. For example, in the automotive sector, such insights can lead to a 20% improvement in return management efficiency by identifying common defect patterns and addressing them proactively.
Advanced RMS Features
Data-Driven Analytics
Leverage our RMS analytics to dissect return patterns, enabling a 30% reduction in inventory overstock and improving forecast accuracy by up to 25%. Tailor strategies based on detailed cost breakdowns and customer return behaviors.
Efficient Inventory Restock
Our RMS facilitates immediate restocking by automating inventory updates, reducing restock time by 40%. This ensures optimal inventory levels, mitigating the risk of stockouts and enhancing shelf availability.
Enhanced Security Protocols
Employ robust security measures like real-time verification and fraud detection algorithms to safeguard return processes. Decrease losses from return fraud by up to 20%, ensuring secure handling of all transactions.
Integrated Logistics
Seamlessly integrate RMS with logistics to expedite return processing by 35%, aligning with transport schedules and reducing handling delays. Optimize fleet operations through synchronized inventory and delivery systems.
Transform Returns Into Revenue
-right-image-1744329706.webp)
Comprehensive RMS Benefits
- Increased Efficiency: Leverage intelligent algorithms to automate returns processing, reducing handling time by up to 30%. This results in faster restocking and less warehouse congestion.
- Customer Satisfaction: Enhance customer loyalty by providing seamless return experiences. Implement hassle-free return policies and real-time tracking, leading to 20% higher repeat purchases.
- Cost Reduction: Employ predictive cost modeling to minimize unexpected expenses in reverse logistics. By optimizing resource allocation, companies can achieve cost savings of up to 25% annually.
- Improved Stock Management: Utilize real-time inventory updates and demand forecasting to ensure optimal stock levels. This approach reduces overstock by 15% and prevents stockouts.
- Enhanced Reporting: Generate detailed analytics on return trends and customer behavior. Use these insights to inform strategic decisions and improve future product offerings, thus boosting profitability.